Innospec chemist Adele Cross champions the benefits of flexible multi-disciplinary teams.
Collaboration between scientists and engineers delivers the right solutions for customers.
Adele Cross, Technical Service Manager for Innospec’s Performance Fuel Specialties business in EMEA, is proud of her team and the work they carry out at the independent and world-renowned UTAC testing facility at Millbrook in the UK.
Adele and her colleagues design and develop bespoke fuel additive packages that offer customers the best performance at the right price point. Her team is a mix of scientists and engineers, and the diversity and depth of their work is staggering.
Although she would not call herself a car fanatic, Adele is dedicated to transforming chemistry into real world performance benefits for the cars on our roads. She is forever challenging her team to be creative in the way they develop new fuel additive packages.
Key to this process is the input from the engineers on her team who will scrutinise reams of data to look for essential insights that can be turned into new performance benefits. Their ability in this area is second to none.
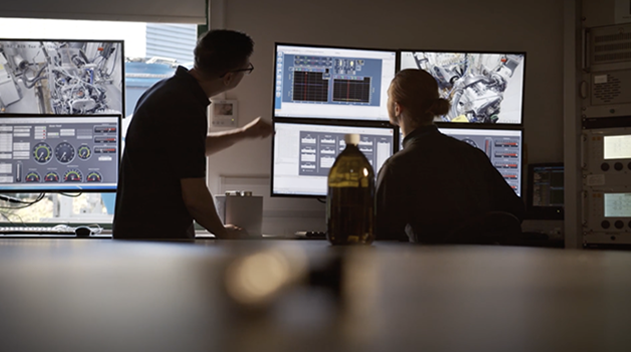
Having Innospec’s own laboratories on-site allows the team of chemists and engineers to test and retest under an exhaustive range of scenarios. The subtle nuances of what a performance fuel additive can achieve are explored in great detail. The team has the understanding, expertise and facilities to investigate test data, examine the product at a molecular level and explore options.
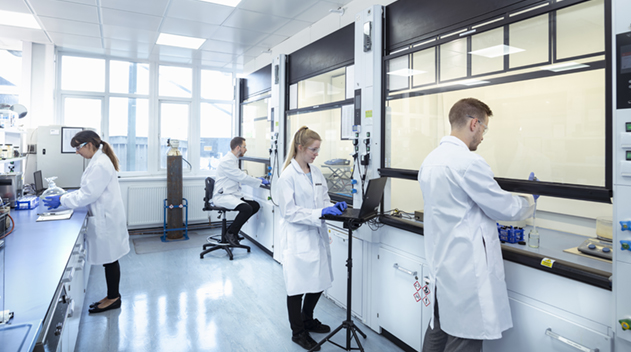
“Having our laboratory located at UTAC gives us unique direct access to the remarkable testing facilities,” explained Adele. “I feel there is real value in my engineers being able to just walk across site for personal meetings with the key people conducting our testing. Being able to view the hardware in person allows us to make more responsive decisions regarding the direction the testing should take.”
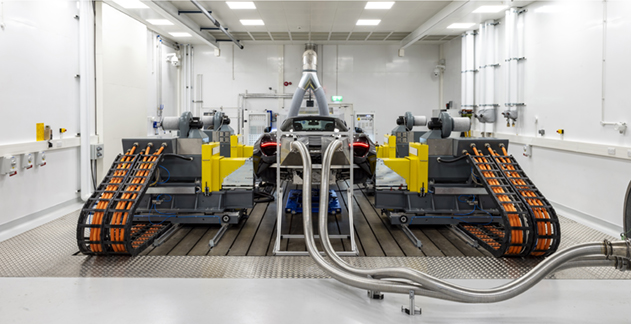
“What makes this process work is the flexibility of our approach and the collaboration we engender across different disciplines. We can revisit the data, repeat tests, and creatively adjust and refine solutions in the lab in real time. After monitoring the performance of a fuel additive using an engine test bed, we may then look at it on a power train or in the emissions lab. If required, we can create real world driving scenarios on the test tracks. There are over 70 km of specialist tracks and surfaces to replicate almost all driving conditions required for real-time and accelerated life-cycle tests.”
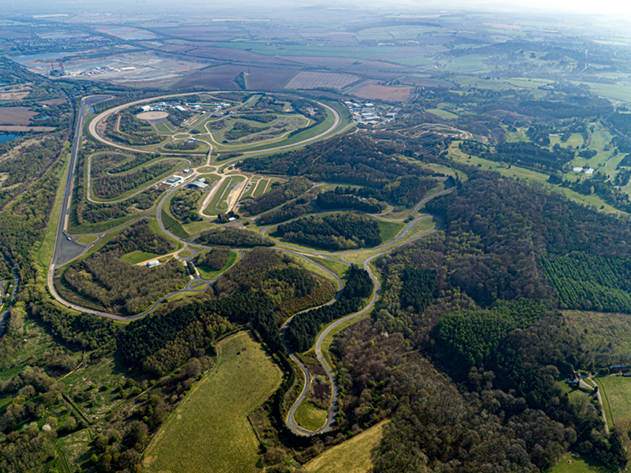
Looking forward, Adele believes the biggest challenge for the fuel industry will remain the environmental impact of fossil fuel powered vehicles. By removing deposits and keeping vehicle engines clean using performance additive packages, Adele’s team are aiming to reduce CO2 emissions and improve fuel economy. With UTAC’s resources at on her doorstep, she is confident her team will continue to make an important contribution to fuel development.
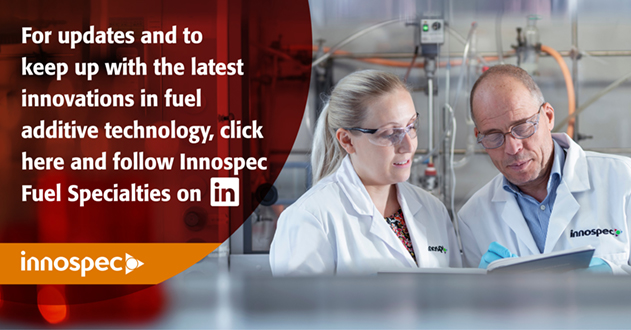